MVR Evaporator
What Is Mechanical Vapor Recompression (MVR) Evaporation?
MVR Evaporator Working Principle
The principle is that the compressor compresses the secondary steam generated by the evaporator, the pressure and temperature are increased, the enthalpy of the steam is also increased, and the steam with increased heat is sent to the heating chamber of the evaporator as the heating steam. The feed liquid is maintained in a boiling state, and the heated steam itself is condensed into water so that the latent heat in the secondary steam is fully utilized, thereby achieving the purpose of energy saving.
The compressor used in the MVR system is the Fan/Blower/Compressor, the selection of which depends upon compression ratio & vapour flow, and it must be made of corrosion resistance stainless steel and mechanically sealed.
MVR technology operates as a closed-loop system, eliminating the need for external heating or cooling sources. This makes it more energy-efficient compared to other methods like steam-heated evaporation.
Industries such as food and beverage, chemical, and pharmaceutical commonly employ this kind of Evaporation due to its ability to evaporate heat-sensitive materials at low temperatures, minimizing the risk of thermal degradation.
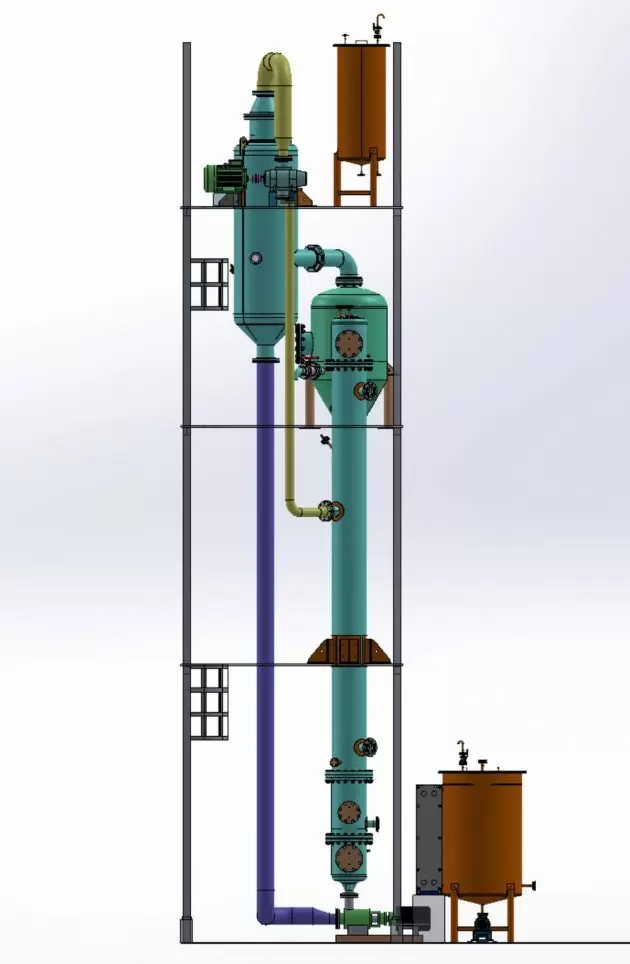
MVR Evaporator Plant Working Process
The Mechanical Vapor Recompression (MVR) Evaporator is a forced circulation evaporator with or without self-cleaning fluidized bed technology or a Falling Film Evaporator without self-cleaning fluidized bed technology. Feed is initially heated by using steam/Thermic Fluid/Electricity in Plate Heat Exchanger; heated feed enters into the calandria and then to the vapor-liquid separator, where vapors & liquid gets separated, low-pressure vapors from VLS enter the MVR Fan/ Blower/Compressor, where it gets compressed to increase the Temperature & Pressure of vapors, compressed vapors then enter to shell side of calandria, where it transfers the heat to feed inside the tube by condensing.
Hot condensate from the Calandria shell is used to preheat the incoming feed in a plate heat exchanger.
The concentrate from VLS is then fed to a settling tank followed by a centrifuge for the solid separation post-evaporation. In the centrifuge, separation occurs in two cycles: Filtration and Centrifuging. The mother liquor is sent back to the feed tank as a recycle stream. The purge is sent to the ATFD feed tank for further Separation of dissolved solid.
The thermal design of an MVR plant requires careful attention with respect to the compressor performance, the composition of the liquid and the required heat transfer area. The compressor design and selection will determine the temperature increase given to the vapor and yields the driving force for heat transfer between the condensing vapor and the liquid at the tube side. The higher the temperature difference, the lower the required heat transfer area (HTA). On the other hand, the higher the temperature increase, the more power the compressor will consume.
Operating compressors will require some attention from plant operation. The equipment is more robust when using root blowers; the needed attention is less than with turbofans. Turbofans have fast-running impellers with high tip speeds that are susceptible to vibration issues when the impellers get dirty. Monitoring the vibration and stopping the fan in time will prevent more significant damage. Experience has shown that MVR units have good reliability when taking care of the compressor.
Benefits of an MVR Plant
MVR Evaporation offers numerous advantages over alternative evaporation processes:
- MVR Evaporator plant consumes less energy: Compared to conventional evaporators, it reduces overall plant operating costs. In the conventional evaporator, most of the energy in the form of steam generated is either lost or partially utilized. In the mechanical vapor recompression process, the entire steam is compressed using the mechanical pump at higher pressure, creating high heat energy for further evaporation.
- Low-temperature evaporation: The process enables low-temperature evaporation, which minimizes the risk of thermal degradation for heat-sensitive materials.
- Reduced operating costs: MVR evaporator significantly decreases operating costs by reducing energy requirements and maintenance expenses.
- Improved product quality: MVR Evaporator helps maintain product quality by preserving the flavor and aroma of heat-sensitive materials and minimizing thermal degradation risks.
- High heat transfer performance
- Compact design
- Environment friendly
- No steam and cooling water required
In A Nutshell
Mechanical Vapor Recompression (MVR) Evaporation is a cost-effective and highly efficient process for evaporating liquids. It is particularly valuable in food and beverage, chemical, and pharmaceutical industries, which necessitate effective and efficient evaporation processes. With its closed-loop system and low-temperature evaporation capability, the MVR Evaporator substantially benefits various sectors.